When the fashion trio threeASFOUR debuted its first collection of 3D-printed clothing, a parade of auburn-haired models marched down a runway at the Jewish Museum in New York City. Their gowns looked both ethereal and geometric—the garb of angelic robots. One dress, for example, was composed of white, angular bubbles that made their wearer look like she had emerged from a very foamy bath.
But the woman who shepherded it down the runway couldn’t sit down, or the dress would shatter. “The model that was wearing it hated us,” says Bradley Rothenberg, an architect who collaborated on the project with threeASFOUR.
Follow Backchannel: Facebook | Twitter
That was in 2013, when threeASFOUR began to realize that reaching the future of fabric might require taking a few steps back. The trio at its helm — Gabi Asfour and his design partners Angela Donhauser and Adi Gil — never meant to create clothing so prone to wardrobe malfunctions. They wanted to do the opposite: stretch clothing to superhero heights. They dreamed of 3D-printing textiles that were bulletproof, fireproof, pressure-resistant, or able to trap heat or cold. In a run-of-the-mill dystopia, the garments they had in mind would fly off the shelves.
That time might be more or less now. At a moment when Silicon Valley’s elite are building personal bunkers, refugees are sneaking across the border into Canada, and Margaret Atwood is once again en vogue, threeASFOUR’s vision is not so far from where the apocalyptically minded have already gone. But where hoarding cans of Doomsday beans is within just about anyone’s reach, achieving sartorial superpowers has proven more elusive.
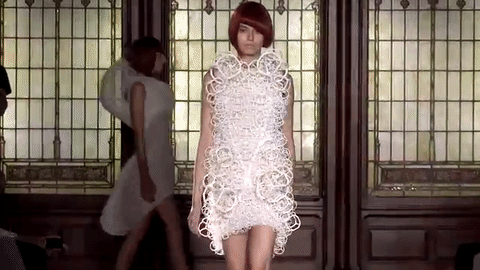
The reason is simple. Thousands of years of refinement have allowed traditional weaving and sewing to produce wearable, durable clothing more efficiently than an upstart method like 3D printing. But that hasn’t stopped the team behind threeASFOUR and other entrepreneurial designers from pushing the limits of fabric to see just how far — and how weird — it can go.
“With fashion there is the potential to control the weave and control the structure to get exactly the properties you want,” says Rothenberg. “The issue is that today, it’s still potential. That’s why I think Gabi [Asfour] is, like, the most exciting person in fashion. We need people like him to push the limits, to show what’s conceivable.”
Gabi Asfour has a cerebral, esoteric bent that soon becomes clear in his work. Since becoming curious about 3D printing around 2009, he has been trying to manipulate the internal geometry of textiles.
Traditional fabric is essentially two-dimensional — strands are arrayed horizontally, vertically, and in crisscross to form a weave. Asfour—who has degrees in mechanical engineering and architecture from the University of Maryland—had a vision, along with Donhauser and Gil, to create “three-dimensional interlocking weaves,” which they would achieve with the help of laser cutting. The desire to mess with fabric’s third dimension drew them naturally to 3D printing.
So far, Asfour says, “the most advanced fabric has been a four-way stretch.” That’s what’s possible with most normal fabric, which stretches along the X and Y planes. 3D printing would allow a material to stretch in the Z plane, Asfour theorized. He figured that such fabric would be more breathable and make movement easier. Best of all, it would eliminate wrinkles.
Asfour and his collaborators started asking around about 3D printing, and those inquiries eventually led to a collaboration with Materialise, a 3D-printing firm, and Rothenberg, who had designed the 3D-printed wings in Victoria’s Secret’s 2013 fashion show.
“When we started, Gabi was just like, ‘Can we make a textile out of this? Can we 3D print a fabric out of this material?’” Rothenberg says from his seat behind a table at his studio in New York’s Chinatown, where he and Gabi work. It turned out to be harder than anyone imagined.
The main challenge was that 3D-printing materials are far more rigid than the fabrics used in clothing. Over and over, they would alter the internal geometry of various materials to add more stretch to them, but once a printer deposited them in layers, those new materials would always shatter. “The practicality at the end comes and kicks your ass,” Asfour says.
As materials slowly improved, however, threeASFOUR worked up to dresses like Pangolin, a collaboration with 3D-printing company Stratasys and architect Travis Fitch, for the brand’s Fall 2016 Biomimicry collection. Pangolin took 500 hours to print, with 10 printers going at once, followed by a painstaking process of assembly. The garment, named after the world’s only scale-covered mammal, looks like something a contemporary Joan of Arc would wear: a dark yet feminine piece of armor. (Björk wore it to open her tour in Australia last year.) To achieve
[Source”timesofindia”]